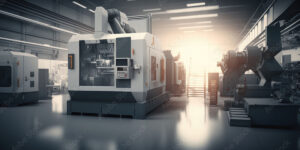
The SyBridge Difference
A single point of accountability across the entire product lifecycle: design, prototyping, tooling, production and after-market services
Our Businesses
SyBridge is designed to fit your organization. We operate under three business units with focused expertise across the entire range of high-precision, multi-cavity tooling; large format molds; and rapid parts and prototyping.
Life Sciences & Consumer
High-precision, multi-cavity tooling
Providing expertise in high precision tooling design and manufacturing across the full product lifecycle for medical devices, pharmaceutical, health & beauty, and consumer goods industries.
- Supporting the largest programs to the smallest details
- Specializing in high-precision tooling
Mobility & Industrial
Large format molds
Serving the automotive, electric vehicle and general industrial markets with design, manufacturing and after-market service and support.
- Expertise in interior and exterior automotive parts and fixture/gauges
- Comprehensive molding capabilities
- Rapid and affordable aftermarket services
Digital Solutions
Rapid parts and prototyping
Leading AI-driven design and digital manufacturing solutions provider to a diverse set of industries.
- On demand manufacturing for custom parts
- Support for rapid prototyping
- Advanced design for manufacturing capabilities
- Global manufacturing network
1
Source
5+
Countries
18+
Production
Facilities
200+
Engineering &
Technical
Professionals
1,200+
Employees
Our Purpose
To reimagine the product design and development process to enable our customers around the world to further their work of improving lives and advancing humankind. Together, we are “bridging the future of innovation”
Our Vision
To be the global leader in technology-enabled design, prototyping and manufacturing solutions for complex, high-precision parts.
Our Values
Customer Focus
We start by listening to our customers and work tirelessly to solve their most complex challenges. We seek to understand their needs and generate deep insights that shape our solutions. At SyBridge, our goal is always to deliver unparalleled value and quality through our solutions, products and services.
Drive to Win
We value having the best people and winning as a team. We hold ourselves to the highest standards of performance. We foster an environment where exceptional individuals with a drive for results, insatiable intellectual curiosity and a bias to action thrive. We value diversity, inclusion and belonging and believe that engagement and collaboration are foundational to success.
Innovation
We are curious about new possibilities and relentlessly challenge the status quo. We encourage creativity, risk-taking and continuous improvement. We embrace technology and seek to continually disrupt pre-existing paradigms. Our legacy will be measured by how we transform our industry and the experiences of our customers through innovation.
Continuous Improvement
We seek breakthrough performance through continuous improvement, lean principles and rigorous implementation of the SyBridge Business System. Standing still is not an option. We expect curiosity about how things are done and a deep need to always make things better – processes, products, services, our industry, and the community at large.
Integrity
We act with integrity, honesty, and transparency in everything we do. We uphold the highest standards of ethics and comply with laws and regulations. We seek to foster a culture of open communication, trust and respect where new ideas and constructive debate flourish.
Over 1 million square feet of manufacturing capacity globally
Leading position in high-value target end-markets
Ranked top-3 toolmakers in North America
We are trusted by
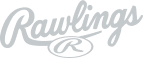
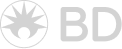



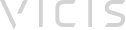