Making customized logistics possible
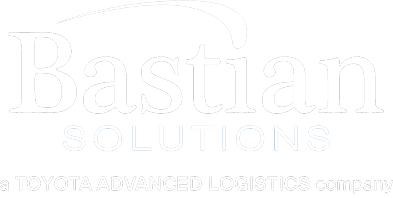
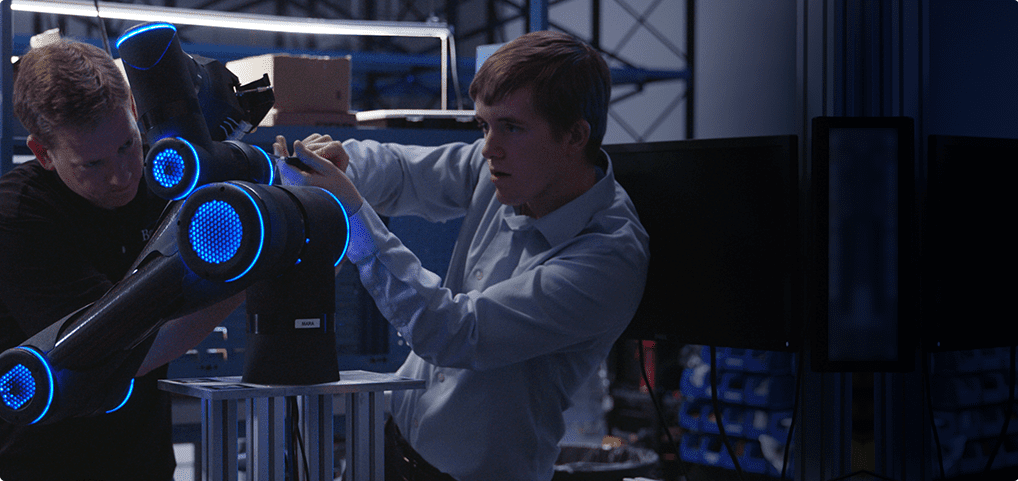
Bastian Solutions envisioned a customizable, next-generation materials handling robot made with additive manufacturing. Fast Radius helped them save $100,000 in production costs by transitioning nearly half the bill of materials to additive parts.
THE CHALLENGE
Using additive manufacturing to enable a customizable solution
Bastian Solutions needed a partner like Fast Radius to make customizable materials handling systems possible.
Bastian Solutions, a leading materials handling company owned by Toyota Advanced Logistics, created a new disruptive materials handler that required an equally disruptive production method — additive manufacturing. Fast Radius made their vision a reality, serving as a close manufacturing innovation partner through the development and production lifecycle.
The Bastian Solutions Shuttle System is an advanced, customizable electric robot arm-and-shuttle combo that autonomously picks and moves a range of differently sized and weighted products. Bastian Solutions created the system in order to solve a complex problem: Retailers need innovative materials handling technology that can navigate tight warehouse spaces, filling orders quickly to meet rising shopper expectations for on-demand delivery. These systems must have picking capabilities that can handle a wide variety of product shapes, sizes and densities.
However, it’s hardly “one-size-fits-all” when it comes to purchasing a materials handling robot. And customization, with all of its retooling, can be expensive. To make this truly innovative advanced materials handling robot and its customizations possible, Bastian Solutions needed the help of Fast Radius and its access to technology partners HP 3D Printing and Carbon® .
MAKING IT POSSIBLE
Rapid iterations and additive production
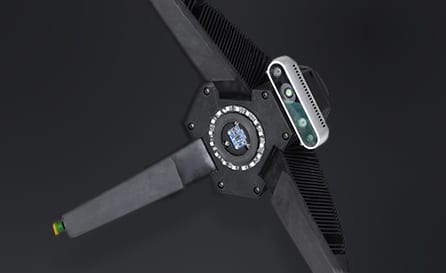
1. Rapid manufacturing of custom parts
Digital manufacturing with Fast Radius completely eliminates the need for tooling. By using industrial-grade 3D printing for critical parts, Bastian Solutions can quickly scale the robot arm for its customers’ requirements. In fact, nearly 50% of the bill of materials (BOM) are made using additive manufacturing in Fast Radius’ Chicago factory. Once the adjusted design is submitted to Fast Radius’s Virtual Warehouse™, Bastian Solutions receives the additive parts in days instead of weeks or months. This helps customers get their new materials handling systems up and running with minimal interruption to their business.
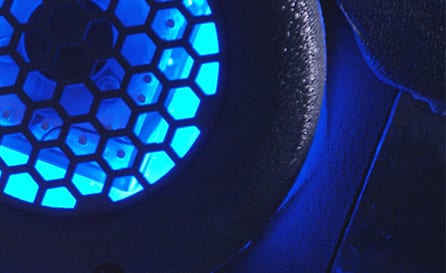
2. A lightweight, energy-efficient machine
In the past, Bastian Solutions’ materials handling robots were typically made with metal. But HP Multi Jet Fusion allowed the company to swap out metal components for ones made with HP 3D High Reusability (HR) PA 12 Glass Beads (a proprietary HP nylon material), making the parts lighter and more efficient to produce. A lighter robot arm means that less energy is required to shuttle it around a warehouse or retail floor. Since the lighter robot conducts less heat while in motion, it requires less energy to cool.
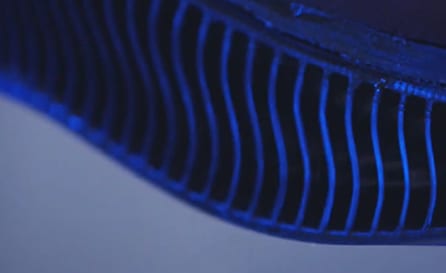
3. A multi-faceted gripper
The gripper on a materials handling robot must be able to securely grab a wide variety of objects in a retailer’s inventory. Fast Radius’s broad additive technology capabilities made it possible for Bastian Solutions to develop a proprietary “Shark Fin” adaptive gripper using Carbon® Digital Light Synthesis™ and EPU 40 material. Carbon’s material enabled the development of a unique set of fingers that are strong but pliable — capable of picking up anything from laundry detergent to lip gloss.
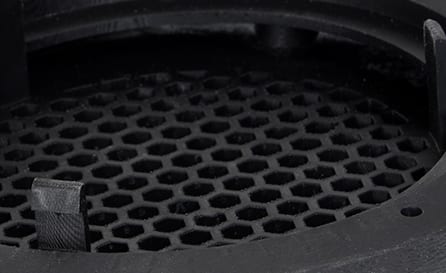
4. Enhanced protective parts
Fast Radius made many of the plating and parts built for support or protection using Carbon DLS. With access to Carbon DLS, Bastian Solutions was able to tap into Carbon’s extensive material library, including EPU 40 and RPU 70, to experiment with different textures, durometers and lattice designs to find an exact fit for their product.
5. Significant project time and cost savings
Making almost half of their BOM with additive manufacturing not only improved the final product, but it also saved Bastian Solutions considerable time and money. By using Fast Radius’s manufacturing innovation platform and team of application engineers, Bastian Solutions was able to design, produce and test hundreds of prototypes in fewer than 20 months. The process cut two years off the project development cycle and saved $100,000 in production costs.
THE RESULTS
By partnering with Fast Radius, the Bastian solutions team developed an innovative, customizable materials handling robot that they can offer at a competitive price
100+
prototypes designed and tested in less than 20 months
2 years
cut from the development cycle
45%
of the final parts made with additive technology
50%
of the BOM made using additive manufacturing
We envisioned that additively manufacturing specific parts would make the Bastian Solutions Shuttle System the most efficient and agile robotic picker available on the market. The additive manufacturing process will enable us to customize each robot picker to fit a customer’s particular warehouse environment.
Gallery
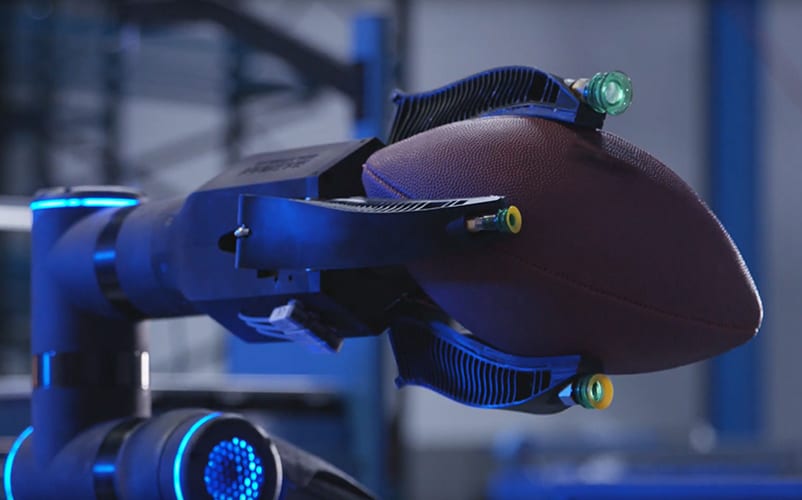
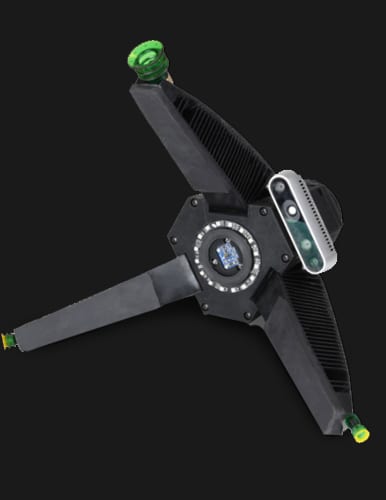
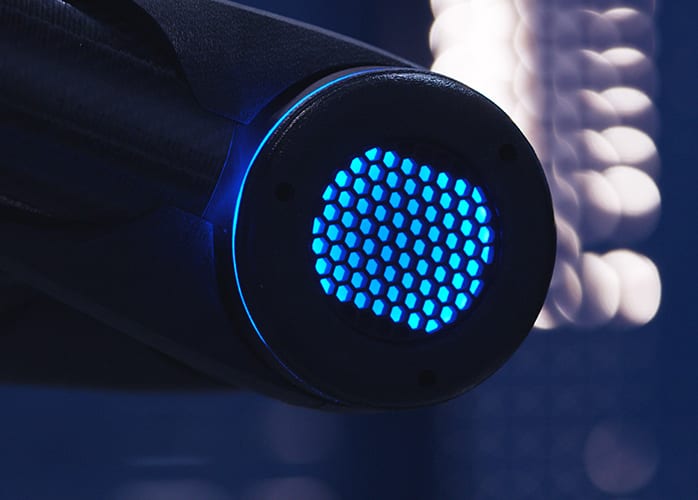
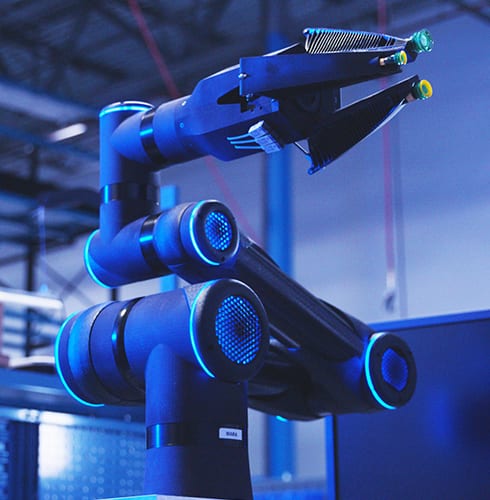